Every day, I am sure to receive either a quality self-audit checklist or a request for a copy of our company's current quality accreditation. Dutifully, I respond with the appropriate fax or mailing in the hopes of satisfying a customer who requires verifiable information that we are "Accredited." As I'm sure many of you are faced with the same ritual, I won't bore you with a detailed discussion of the process; but suffice it to say, the process can turn into an administrative part-time job.
What does it all mean? Is all this administrative work actually accomplishing anything? Are we any better at checking gage blocks, ring gages, or setting discs now that we are accredited? Can we prove this? The answer, of course, is "Maybe".
As an A2LA-certified company, we have run the gamut of audits, self-assessment, and proficiency testing. Though we've always performed round robins with the other industry leaders in our field – always with a touchstone at NIST – we weren't under the pressure we are now to continually prove the reliability of our results and processes at stated intervals to an A2LA or company auditor. Today, we feel this pressure and the results have been positive.
Meeting the Demand for Testing
In response to the A2LA demand that internal proficiency testing be performed at stated intervals, we've developed the hardware and software necessary to facilitate the automatic downloading of our measurement readings from the digital display to a specially formatted spreadsheet. Every week, each metrology lab team member is notified automatically by the lab computer when proficiency testing will be performed. Each technician is then responsible for verifying the accuracy of his or her calibration equipment and technique using a predetermined procedure that uses lab masters with a history of calibrated readings. If a substantial deviation in the readings occurs, the equipment is taken out of service and investigated further to determine the cause of the deviation.
Note: This process verification occurs automatically anyway as soon as we measure a customer's gages for the second time. Though less formal than our weekly process checks, the actual process of repeat comparative measurement yields the same results by raising the similar process flags.
Today I can use my computer to view the quickly accumulating proficiency testing data on our lab calibration processes. When requested, this data can be supplied to auditors as evidence of proficiency testing and tracking. Additionally, lab temperature is recorded automatically and downloaded to a spreadsheet where it can be viewed by interested parties. Though our lab also engages in inter-laboratory comparisons (round robins), it can take many months before the data is available. With weekly proficiency testing and less formal daily process checks, we have a reliable and up-to-date indicator that can identify any problems we may be having with our process.
Of course, we use the same automatic data transfer system when we generate our certifications. This system has virtually eliminated the risk of transposition errors as well as the need to enter readings manually into certification software, and lead times have been reduced by an entire day.
About the Author
Rob Edmunds III has a Bachelor of Science degree in Mathematics and Business from Villanova University. Involved with many facets of the gaging industry, he also participates in national and regional industry associations. Currently vice president of Edmunds Gages, he can be reached during normal business hours at Edmunds Gages or via email at REdmundsIII@edmundsgages.com.
Towards a Better Lab
These process improvements were stimulated, in large part, by our need to accurately and efficiently record and document required data at pre-set intervals for quality accreditation purposes. The end result has been a more efficient and well-documented gage lab.
The famous Wall Street tycoon J.P. Morgan once said, "A businessman's greatest challenge is to take a problem and create an opportunity from it so that, in the end, he is in a better position for having faced it." Though I'm quite sure he wasn't thinking about quality issues for a modern industry, his point is well taken. The increased burden on modern industry to draft procedures, develop and defend uncertainty budgets, document readings, proficiency test, etc. certainly has a real cost. However, because this quality revolution is no longer an option, it may be a good time to "reinvent yourself" by taking a hard look at your procedures and processes in light of these new demands.
Maybe Jefferson was right, a little revolution is a good thing.
TheLogistics of Proving Quality
As seen at: NEWS & ANALYSIS@metrology world.com
Setting up the methods and making the time to prove the reliability of results at stated intervals should be standard operating procedure in this "quality revolution."
By: Robert Edmunds III
Edmunds Gages
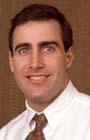




A New Dimension In Precision Measurement
.
(860) 677-2813

Toll Free 877-521-5818