KNOW YOUR GAGE-BLOCK BASICS
In this kickoff to Quality's Metrology Toolbox series, an expert tells how to work with gage blocks
By Robert Edmunds III
Gage blocks have been used by metrologists for more than 85 years, yet they have not changed tangibly in design, application, or even accuracy in the past 70 years. Though gage blocks – defined as square, rectangular, or round shapes (manufactured of steel and other materials) that have flat and parallel opposing sides – are simple compared to most types of sophisticated gaging today, they are still the industry-standard length masters.
Gage blocks are used daily in a broad spectrum of applications, from measuring parts loosely on the factory floor to measuring to millionths in an environmentally controlled metrology laboratory.
Although gage blocks are quite familiar to metrologists, there are still misconceptions and considerable misuse in the field – and it is helpful to be reminded of the basics. This article will discuss the conditions necessary for optimum measurement, clarify the terms wringing and stacking, discuss how to wring gage blocks correctly, and provide an update about coming changes in gage-block specifications.
Stacking and wringing
Stacking gage blocks involves choosing the right combination of blocks to make a set up to proper size. The goal is to use as few gage blocks a possible because each "wring" adds some deviation to the set up. For example, if the set up is for 2.8763 in., begin with the digit farthest to the right. Your first block will be 0.1003 in. Again, working from the right side, the next block will be 0.126 in., then 0.650 in., and finally add the 2 in. Now you have 2.8763 in. It's simple!
Wringing gage blocks together, which means combining them end-to-end to add their measurement values, is the real key to accurate gage-block setup and use, and it's also the most misunderstood concept. The phenomenon of wringing gage blocks so they seem to "stick together" occurs for two reasons. First, there is an adhesive action because of an ultra-thin film of oil or moisture between the blocks. Second, there is a molecular attraction or bonding, between the blocks because of the very flat and parallel mating surfaces. That's why the better the block geometry, the better the wring will be (see "How to wring gage blocks step-by-step").
Once you're familiar with stacking and wringing, there are three gage-block preparation steps you should take each time you are going to make a measurement.
Clean and demagnetize.
Using clean and demagnetized gage blocks is paramount. A gage block that has grease or grime on it will be inaccurate. Most clean-up jobs can be accomplished by wiping each block with a soft, lint-free cloth moistened with mineral spirits. You must also demagnetize all blocks that retain a magnetic field. Good electronic demagnetizers and gauss gages are common catalog items today.
Eliminate nicks and burrs.
Gage blocks require good overall geometry to measure accurately. Nicked, burred, or scratched measuring faces will not wring together well and most likely provide anomalous readings. Deburring the measuring faces of steel gage blocks by lightly "swiping" them along the face of a clean, flat, serrated, Arkansas or granite stone is ideal, while using clean mineral spirits as a carrier. This procedure, if performed correctly, will not hinder the quality or integrity of the gage blocks. Note that different block materials will require other types of deburring stones.
Maintain temperature.
Varying environmental temperatures affect material size, especially when using two different materials in your application. For example, if the gage blocks are steel and the part is aluminum, thermal expansion/contraction causes the two materials to move at different rates of speed. If the temperature is fluctuating as well, the problem is compounded. When measuring to millionths in a true metrology laboratory, the temperature of the room, and all its contents, is set at 20 C and is held within 0.25 C. Ted Doiron, a physicist in the precision engineering division of the National Institute of Standards and Technology, Gaithersburg, MD, often refers to something he calls Doiron's Law of Dimensional Metrology: "The guy with the best thermostat wins!" It is simple, but very true: in millionths measurement, temperature is everything.
Future of the gage block
Updates in gage-block specifications (in view of the cancellation of Federal Specification GGG-G-15C), and the push for the United States to be more ISO (International Organization for Standardization, Geneva) compliant, have led to a review of the ISO standard for gage blocks, ISO 3650.
Although the United States will not adopt the ISO 3650 standard, the American National Standards Institute (ANSI) is now in the process of changing and updating our ANSI gage-block standard, B89.1.9. I am a member of this and other working committees. Among the proposed modifications is gage-block grade names. Another suggestion is to make the size tolerances more open and bilateral, i.e., +/-6 in. rather than +4/-2 in. This will refer to and include all the points on the gaging surface, rather than just the one reference point that the old standard required. This change should lead to better block geometry because the variation in length tolerances (formerly called parallelism) will be tighter.
Because of the several added steps in the new procedure, along with the additional number crunching, you will probably notice an adjustment in pricing from your metrology laboratory.
The new process will take nearly twice as long as the old one. The benefit to you is that these changes will result in more accurately calibrated gage blocks and the documentation you receive will be more in-depth and ISO compliant.
How to wring gage blocks step-by-step
Clean the blocks by applying a small amount of mineral spirits to a clean, soft, lint-free cloth.
Lay another piece of clean, soft, lint-free cloth on a flat nonabsorbent surface.
Place two drops of clean, filtered, light oil on one area of the cloth.
Take one of the clean blocks and place it with the measuring face down on the cloth, rubbing it gently in the oiled area.
Move the block to an un-oiled section of the cloth and move it in a figure eight motion to clean off the excess oil. (When cleaned correctly, the oil should only be visible as a slight discoloration to the block surface).
Slide the gage block with light pressure onto another clean gage block.
Wring the block half out of engagement and then back into the matched position in a circular motion.
Continue this wringing procedure until the desired setup is complete.
With practice, wringing gage blocks becomes second nature. To check your skill level while learning, wring two 0.500-in. blocks, with known deviations, together. After letting them "soak" back, or return, to ambient temperature, compare the setup to a 1-in. block, with known deviation, under a high-magnification bench comparator.
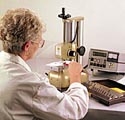




A New Dimension In Precision Measurement
.
(860) 677-2813

Toll Free 877-521-5818