Loose Tolerance Are Ok_
A product's performance is often influenced by the clearance, or in some cases by the preload, of its mating parts. Achieving consistent and correct clearances and preloads can be a challenge for assemblers. Tight tolerances often increase assembly costs because labor expenses and the scrap rate go up. The tighter the tolerances, the more difficult and costly the component parts are to assemble. Keeping costs down while maintaining tight assembly tolerances can be made easier by a process called selective assembly, or match gaging.
By: Richard Mierzejewski
Manager of Applications Engineering
Edmunds Gages
To match gage for selective assembly, one group of components is measured and sorted by dimension prior to the assembly process. One or more other components are then measured and matched with a presorted part to obtain an optimal fit to complete the assembly.
By focusing on the fit between mating parts rather than the absolute size of each component, looser component tolerances can be allowed. This reduces assembly costs without sacrificing product performance. In addition, parts that fall outside their print tolerance may still be useable if a mating part for it can be found or manufactured, thus reducing scrap.
Not all products are candidates for selective assembly. When tolerances are broad or clearances are not critical to the function of the final assembly, selective assembly isn't necessary. Selective assembly works best when the clearance or preload tolerance between parts is tight, usually under 0.0005 inch. Selective assembly is also a good strategy when a large number of components must be stacked together to form the assembly, as with an automobile transmission system. In that instance, holding tolerances tight enough for random assembly while maintaining the correct clearance or preload would be impractical.

Match gaging allows for less stringent tolerances of precision parts and results in better assembly of complex components
Selective Assembly in Action
Selective assembly is crucial for cost effectively assembling a rotary vane compressor. The clearance tolerance between the vane and its mating part, the cylinder, must be maintained within 0.0002 inch. An automatic gage measures the height and thickness of the vanes. Rejected parts are removed from the gage via an exit chute. The remaining parts are sorted into 10 magazines according to size and then transported to the assembly area.
During assembly, the cylinder is measured for overall height and vane slot width with another gage. Based on the results of these measurements, the gage selects the correct sized mating vane. A computer linked to the gage analyzes and displays all measurements and stores the data for statistical process control charts and calculations.
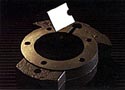
Match gaging is particularly suited to assembling motor vehicle transmissions. Transmissions have too many components to be randomly stacked and still achieve the correct preload. To machine each component to a tighter tolerance would be prohibitively expensive. Even if the individual parts are within their own tolerances, the total length of the gear stack assembly can vary considerably. Moreover, the housing for the gear stack can also vary slightly within manufacturing tolerances. So if both the housing and the gear stack are made to their own specifications, they still may not yield the correct preload at assembly.
A system of two gages solves the problem. A housing gage mounted on an overhead, counter-balanced arm measures the interior dimensions of the transmission housing from the face to the bottom of the two bores where the gear stack will go. A second, larger gage mounted on a cantilevered, counterbalanced are comes down over the gear stack and sits on the mating face of the stack. The motor-driven gage rotates the shafts to correctly seat the bearings and gets accurate dimensions from the top of the gear stack to the mating face.
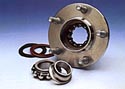
Data from the two gages is sent to a computer, which calculates what size shims need to be added to the gear stack to adjust the clearance and provide correct preload when the housing and gear stack are assembled. To ensure accurate measurements, the gages are regularly calibrated with two sets of masters that duplicate the actual dimensions of the housings and the gear stacks.
Other candidates for match gaging are bearings, such as those used for automobiles. In this case there are three critical measurement areas: the outer races, inner races d balls. The balls are sorted by size and matched at the time of assembly to the inner and outer races.
Succeeding With Selective Assembly
To successfully implement match gaging, the assembler needs to stand back from the manufacturing process and look at the total assembly process. The size and the geometry of the mating components must be measurable and controllable. When the fit of components is not critical or tolerances are less exacting, match gaging may not be beneficial.
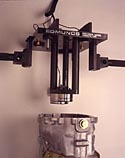
However, when an assembler is able to incorporate selective assembly into its process, the cost savings achieved in broader manufacturing tolerances and scrap reduction is significant. In addition, the quality of the end products enhanced, because the selective assembly process provides perfectly matching parts.
Reprinted from Assembly Magazine




A New Dimension In Precision Measurement
.
(860) 677-2813

Toll Free 877-521-5818