Differential Carrier
Gage Parameters
GAGING SYSTEM: Electronic (LVDT)
OPERATION: Automatic
NUMBER OF CHECKS: 5
READOUT: CAGTM
CLASSIFICATION: Good/Reject
FEATURES: Automatic measuring system to provide 100% inspection of a turning process with Feedback to multiple Okuma lathes.
The Solution
Automatic post process measurement immediately after the part has been produced, and before the next part is machined, closes an often open loop in the process with automated dimensional feedback. In this application, a robot is used to load and unload the Okuma lathe. The same robot places the outbound machined part into an Edmunds Gages automated gaging system. Here, the part is handled, measured, and returned to the deposit point by Edmunds Gages. Likewise, an Edmunds CAGTM (Computer Aided Gaging) system records, displays and reports the dimensional information back to the Okuma controller for instant feedback of what was produced. The next part machined is brought right back to process size, all without an operator making a determining judgement. In the unlikely event a part exceeds a process tolerance, an alarm signal is sent to the Okuma to stop the turning process before another process limit is violated. And as a quality inspector, the Edmunds CAG will also determine if a part print limit has been exceeded, signaling the robot to distribute the part into a reject area.
The Challenge
Turning, in a production process, can often be a trying task especially when the tolerances are controlled very close, and the production rates are very high. Add to that a cast iron part, with interrupted cuts, and changeable inserts as cutting tools. Keeping the scrap rate low, while minimizing labor, and maximizing part count per tool become three very important issues to consider. But how can one control the process, with minimal labor, and max part count without sacrificing quality?
The Result
The benefits of Edmunds Gages post process feedback gaging are plenty. First, because an operator is not required to make judgement decisions, overall labor within the process is reduced. Now the operator of an entire line is simply monitoring the output of multiple machines, rather than typically one machine. Next, because a limit can now be applied to this specific process, the amount of remaining material can be better controlled for subsequent processes down stream. And third, because of the Edmunds CAG having (2) sets of limits (process and part print) the quality of the parts are improved by removing rejects at the process rather than at the end of the line. Scrap is reduced or eliminated.
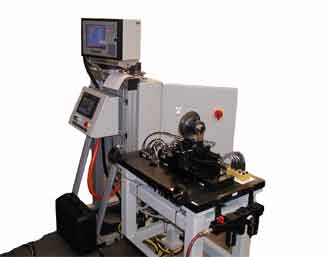
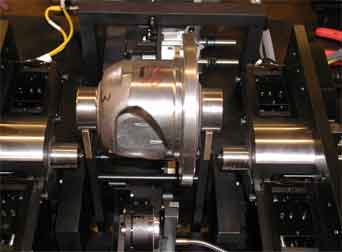
Keypad Control
Operation of the CAG system is achieved by a 16-position keypad in conjunction with a menu-driven LCD display. Depending on the type of application, and the software developed for it, the operator can be told which task to perform, or be given a choice of actions. In certain applications the operator will answer YES/NO or key in the appropriate number, then ENTER, and the system advances to the next step.




A New Dimension In Precision Measurement
.
(860) 677-2813

Toll Free 877-521-5818