Gaging Gears For Harley-Davidson
By Donald B. Dobbins
Senior Technical Editor
Reprinted from Quality in Manufacturing
Recently I had an opportunity to sit down with Donald L. Baird, vice president, engineering, and Mark Krzewinski, applications engineer, at Ellison Machinery Company, Pewaukee, WI, to discuss two manufacturing cells that Ellison Machinery installed at Harley-Davidson, Milwaukee, WI. These lines are used to produce six different transmission gears. The first cell began operation about two years ago. The second cell went on-line in February.
“Perhaps as long as 15 to 20 years, Harley-Davidson bought two gear manufacturing lines from a company by the name of Suga,” Baird says. “There were four machines in each line plus a series of elevators and gravity chutes that delivered components to spindles for machining. When these lines were installed, they were considered state-of-the-art, and they ran successfully for years and years.”
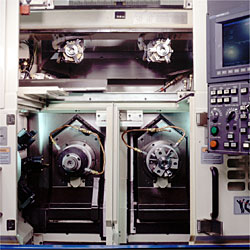
This twin-spindle Okuma lathe is used to machine both sides of a gear blank at Harley-Davidson. Gantries are used to load and unload parts. An Edmunds Air Gage is used to measure every part and send corrections back to the machine control to compensate for any deviation from tolerances.
These machines were described as “semi-CNC machines” by Baird, who says they often were called peg-board machines. When they were introduced, these machines were considered pretty far advanced because a “programmer” could make them go through various iterations and hit hydraulic stops based upon the peg-board assembly, which determined how a machine was going to process workpieces.
“Elevator mechanisms were used to transfer parts onto gravity chutes to send them from spindle to spindle. That was rarely done outside of what I’d call automotive installations,” Baird explains. “Automakers had been using that type of equipment for 50 to 60 years, maybe longer, but for a motorcycle builder with a comparatively small volume, this represented a big leap forward.”
Of course, time marches on and a lack of flexibility and the need for additional processes to make up for the lack of defined accuracy those machines were capable of holding led to Harley’s decision to replace them with modern, high-tolerance manufacturing cells, he says. “If we had done a statistical analysis of that former process,” Baird says, “it probably was capable of holding maybe 0.010_. With that type of in-process capability on their turning equipment, they had to employ a lot of other machines that normally wouldn’t be involved, or perhaps have engineers in the line to remove extremely large amounts of stock to make up for the lack of accuracy in upstream operations.”
A better way
The Okuma machines that Ellison installed can hold tolerance of at least 0.001_. “Statistically, they’re good to half-a-thousandth,” Baird says. “We’ve done demonstrations on that type of equipment with in-process gaging where, if we’re running in a metric mode, we can hold ±4 microns successfully.”
Downtime in the Suga machines and unavailability of repair parts because the builder had gone out of business prompted Harley engineers to look for a better production technique.
Before Harley-Davidson selects new production equipment, they form a committee of maybe 10 or 12 people from various segments of their engineering and manufacturing areas to look at different ways to produce the parts they will be running on the new lines. “They have their predictive change of engineering methods going on at the same time so that group could swell to twice that size during the time when they are trying to assess model changes or modifications for the next five or six years,” Baird says.
This photo shows the second lathe operation. There is a raw forging in the spindle and it is ready for machining.
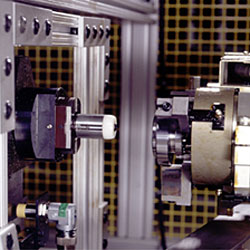
New lines
When Harley decided to upgrade its first transmission gear line, it chose an Okuma twin-spindle CNC lathe with dual gantry loaders/unloaders. “They are using the twin-spindle lathe to machine both sides of a gear,” Krzewinski says. “They can do that in one operation, hands free, using the gantry loaders.
“The right gantry arm will load the first spindle with a green forging and the lathe will finish the front face, rough the bore, and finish the bore,” Krzewinski says. “The gantry then will pull this part out, load a fresh part, and take the half-finished part to what we call a turn-around station. Next it will turn the part to the back side, which hasn’t been machined.
“Now, the left gantry will take the half-finished part and place it in the left side of the lathe. The lathe employs OD chucking on the right side and ID chucking on the left station,” Krzewinski points out. “Because the bore is finished, concentricity shouldn’t be a problem. The first face is used for a datum plane. Next the lathe will finish the last side and the diameter.”
After the lathe has finished the part, the loader picks the part off the spindle and loads another part onto the left station. It then takes the finished part over to the Edmunds Air Gage located at the side of the lathe. Here it will orient the part into a horizontal position, and lower the part onto the air gage. The air gage will measure the part and send an RS-232 message back to the Okuma control. This signal can be used to execute an offset change in the tooling, if required.
After the part is machined in the second spindle the gantry moves over to the left of the work cell and is shown in the process of putting the finished part onto the Edmunds Air Gage for checking the bore.
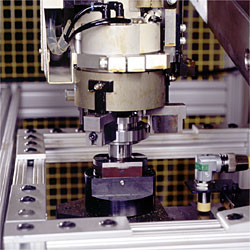
Although every part is gaged, the system is programmed so that it will accumulate measurements of three parts and then wait for four or five parts before it sends back an offset. This avoids the possible problem of hunting or cycling back and forth that could occur if every part were used to correct the next one.
“The benefit of gaging every part,” Krzewinski says, “is that one operator is running this line (it’s about 80 feet long). A single operator is responsible for processing parts from green gear forgings through the Okuma, on which he finishes the bore and rough turns the diameter. Depending on which gear it is, it will be sent through a broach, a profilating machine, a hobbing machine, and then it’s ready for heat treating. Plus, there’s some other equipment as well.
“The advantage of the gaging is the operator can walk away from the Okuma area where the boring and turning takes place, for a long period of time. There also is redundant tooling on that machine. Like any other company, Harley-Davidson is trying to increase production — I think they’re trying to almost double it. They’re also trying to satisfy several other things, such as maintaining or exceeding quality, lowering labor costs, and increasing production. With the Edmunds gaging they can do it all.”
“Another requirement,” Krzewinski says, “is for fast changeover between parts. Each one of those gear lines will do six different gears. The requirement is a 10-minute changeover for the Okuma equipment, which includes workholding, changing all the air plugs for the Edmunds, and changing programs.”
“Sometimes there’s a minor tooling change necessary,” Baird says. “Typically the changeovers are just programs. The new program tells a tool to do something different. Even if there’s a workholding constraint, they can change a set of jaws, call up a new program and they’re producing a new part. Their old system really was inflexible. They could have been looking at an hour or two changeover on their previous line and still not have the capability the new one affords them.”
Cell development
Ellison Machinery worked closely with Harley-Davidson in selecting equipment and marrying the various cell components. “We integrated the Edmunds gaging into the cell,” Krzewinski tells QM. “We specified on the order to Okuma that we were going to use gaging. There is an option called RS-232 post-process gaging, which simply is just software and a port. Setting that up is fairly easy. I worked with Edmunds in Connecticut. I like dealing with them directly.”
“We commonly provide a machining system with integrated gaging,” Baird says. “These gages are expensive but they work well and they have a very good durability record. I’d say we have four or six projects per year where we’ll furnish Edmunds as the gage of choice. We also work with other gage companies. We’re not exclusive with any of them.
“Actually,” Baird continues, “if we were picking gaging equipment ourselves and weren’t being driven by the customer, we would lean toward Edmunds because we have in-house knowledge of how to deal with problems that may arise. Usually there will be a fair amount of problems — any time you have two computers communicating with each other and their operating systems are alien to each other, you have to exercise your wits to get them communicating correctly.”
“All of the components of the system were shipped to us here and we assembled the system for testing and runoff,” Krzewinski says. “We’ll have a statistical runoff here, which is spec’d out in the purchase order. Usually this is a four hour run, but sometimes the purchaser will specify an eight hour run — with no stoppages.”
Once the runoff is completed, Ellison Machinery tears down the machine, packages it, and brings it to the customer’s plant. There it is reassembled and another runoff takes place.
Transmission gears are shown in four stages of completion: green forging (upper right); after the first side and bore have been finished (lower right); after machining has been completed (lower left); and the finished gear after hobbing, broaching, heat treating, etc.
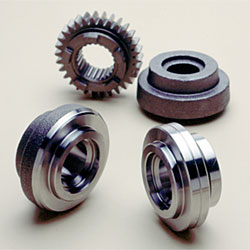
“That’s a speculative group and their engineers probably would be somewhat involved in that,” he adds. “However, their design people would be the ones feeding information into them. That way, if they buy a machine tool system, it has the flexibility to incorporate the changes they would be considering. They do not want to be left in a position where the equipment they bring in is only a five-year solution. They want a 10- to 15-year solution for their production problems rather than just a short-term solution for an immediate problem.”
Training
According to Krzewinski, training can be handled in a number of ways. “With this system,” he says, “we contracted with Edmunds for two days of training. Harley opted to wait until the machine was on its floor and then they brought somebody directly in from Edmunds to do the training.
“Being the integrator, and taking this system from cradle to grave, I was pretty familiar with the gage and did some fairly extensive training on it as well. The in-depth training where they really want to get deeper into the gage, is where Edmunds can provide the needed expertise.
“The lathe, the gantries, and the gage really are a whole system so training has to deal with this equipment as a system,” Krzewinski says. “Operators have to be familiar with the inbound operation where the process starts, with programming the gantry, mechanical training such as changing over workholding devices, changing over programs, setting up the gage, and qualifying the gage.
“Maybe a month or so after runoff in the customer’s plant, we go in for some follow-up training for a day or two,” Krzewinski says. “As with any new system, we can’t possibly answer all questions until it’s in full production. What I typically tell the operators to do is to make a list. Being local as we are, I can easily come back in and work through some of their problems.
“With the complexity of automation and machine tools, we need to do that,” Krzewinski said. “We need to follow up with customers, not drop ship a machine and hope that they understand it. Our customers appreciate that.”
An overview of an Okuma lathe with dual gantry system and Edmunds Air Gage producing transmission gears at Harley-Davidson.
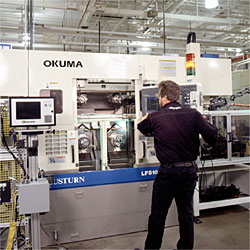




A New Dimension In Precision Measurement
.
(860) 677-2813

Toll Free 877-521-5818