MEASURING TAPERS
(Farmington, CT) Tapered fits are found in numerous applications. The engagement of two mating tapers makes a positive locking arrangement in two directional axes a perfect solution for dynamically accelerated parts. Engines use tapered fits on crank-shaft and flywheel junctions. Gas or fluid valves use tapered shafts and bores for their sealing properties. Orthopedic components use tapers for alignment, location and strength of fit in human body parts. And the international machine tool industry has adopted tapered tool holders as quick change tooling systems without loss of location, which can cause harmonic distortion in the metal cutting process.
By: Jack Gaughan
Manager of Custom Gaging
Edmunds Gages, Farmington, CT USA
Despite their proliferation, the measurement of tapered components is the nemesis of many a manufacturer, whether they are shafts with tapered external diameters, or disc shaped parts with tapered internal diameters. The primary inspection methods have been "gage lab" based and not adept for shop floor production measurement. Some of these methods include measuring the depth of multiple balls in a cone, sine plate setups, and roundness machines.
One of the most common production practices of determining a good taper from bad is a trial and error method call "blueing". Blueing is a process which uses a precision "master taper" or part having its tapered feature manufactured to more stringent tolerances on size and angle than the actual workpiece to be measured. In use, the master taper is lightly and evenly coated with a film of dycom or indelible ink, and then inserted into the mating tapered workpiece. A slight twist of the joined master and workpiece is given, then the master removed for visual inspection.
The methodology is to witness an even distribution of ink in the workpiece, or an even removal of ink from the master. The "percentage" of ink distribution or removal is how the accuracy of the taper is graded. A 50% blue process would mean the master and the workpiece touched at 50% of the entire circumference area of the surfaces. Angle variation can be detected as ink is removed from the master at either of the ends of the master taper, as opposed to across the entire lateral surface. Geometric conditions such as roundness are detected from ink removal around the master's circumference. Another method of blueing includes rolling the master taper on a piece of paper after insertion in the workpiece for one dimensional inspection of the results and record keeping.
However, with tolerances continuously getting tighter, particularly the machine tool standards ISO 1947, one might ask themselves these simple questions: With the user of the master taper being an integral part of the inspection procedure, will the same results always occur? Or, more importantly, can two operators duplicate the measurements? What if the ink is not applied evenly, or the pressure at which the master is twisted in the workpiece is not constant, will the same results appear? The common thread to all these questions is one: How else can tapers be measured easily and economically?
Air gaging has become one of the most economical and reliable solutions for fast accurate, non subjective measurement with variable data as a result. The relatively low cost of such tooling, combined with self cleaning properties of air tooling and the serial output from today's digital air to electronic columns, offer distinct advantages over more flexible universal type gages or "jury rigs". They are also fast, accurate, repeatable, and suitable for shop floor production use.
The design of the most basic air gaging tools for tapered workpieces begins with a measuring device known as an air plug for internal bores or an air ring for external shaft measurement.
Each of these types of tools are grouped into two categories: one for size and one for angle. A typical tapered size tool usually consists of a single air gage circuit. This circuit consist of two open orifices which are diametrically opposed, allowing air to blow against the workpiece on the centerline of a diameter. In a size tool, the location of the circuit coincides with the gage line dimensioning of the product being measured. Since the location of the gage line is often related to an adjacent face, a size tool includes an anvil to seat off that face and stage the air circuit at proper elevation.
The second type of tapered air tooling is a tapered angle tool. This tool consists of two or more measuring circuits. The location of these circuits are usually spread across the greatest distance in the length of the part. Each circuit measures an effective diameter, however each of these diameters is then compared to one another to determine the variation of the angle from nominal. Since the angle tool uses arbitrary circuit locations, this tool seats off the tapered surface of the part.
The comparison of each of the diameter circuits then provides the variation in the workpiece angle. As the large end diameter measurement increases and the small end diameter decreases, then the angle is considered to be increasing. When the opposite occurs, the large end diameter decreases, and the small end diameter increases, the angle is considered to be decreasing.
Because both type tools function using two point diameter measurements, rotation of the air tool will also indicate the geometric conditions of roundness. And if additional circuits are added to either tool, the tapers shape can also be viewed as barrel or bellmouth shapes. Economics of the inspection usually regulate the number of diametrical measurement planes with two circuits being the most common for angle only measurement and three for angle and straightness.
One must remember however, that the application of an air tool to a product, whether it be a tapered size or angle tool or just an ordinary bore plug or air ring, requires that the total change in size witnessed by the tool is less than .005" due to the physical characteristics of compressed air.
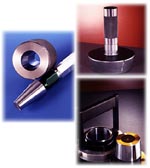




A New Dimension In Precision Measurement
.
(860) 677-2813

Toll Free 877-521-5818