Rotary Compressor Top Flange Setting Machine
Gaging Parameters
GAGING SYSTEM: Electronic (LVDT) OPERATION: Automatic
NUMBER OF CHECKS: 3
READOUT: CAGTM
CLASSIFICATION: Good/Reject
FEATURES: Automatic measuring and setting by monitoring the shaft/roller assembly throw dimension, and the flange/cylinder position.
The Challenge
Simply centering a circular workpiece may not be an unusual task. But, setting the position of a rotary compressor flange and its mating cylinder so that each can accept a variety of eccentric shafts – automatically and accurately – certainly is. Further, automatically tightening the screws that secure the flange and cylinder to a specified torque, while keeping the parts in position, is a most challenging task.
The Solution
Automatic measurements and settings are achieved on the top flange setter with data from the Edmunds CAGTM (Computer Aided Gaging) system. The task is performed by monitoring three independent measurement cycles. The first measures the eccentric shaft with its mating roller in place for the maximum throw dimension on these parts. Simultaneously, the pre-assembled flange and cylinder are clamped in the measurement position and their retaining screws are loosened.
The second measurement determines the position of the flange and cylinder in the X-axis and sends a signal to servo-driven slides in that axis to move the flange to the proper center position.
The third measurement uses the throw value of the shaft and roller assembly to move the servo slides in the Y-axis to achieve a particular gap between the parts. The screws are then tightened to a specified torque value and the cylinder and flange measurements are reviewed again to verify the part remained stationary during the screw tightening process.
The Result
The benefits of Edmunds CAG-driven flange setter are three-fold, each contributing to increased production capability and/or customer satisfaction. The automation of the setting process, enabled by accurate dimensional data from the CAG, eliminates the cost of manual measurement, setting, re-measuring and possible adjusting.
The consistently tight tolerance of the gap setting, assured by the Edmunds gaging system, promotes better product performance and overall quality. And, perhaps of greatest impact to the bottom line, CAG-driven flange setting increases production rates from 25-30 assemblies per hour to 200 per hour – parts off the line 1000% faster, set at .005 mm tolerance – a profitable benefit from Edmunds' advanced gaging application technology.
CHK DESCRIPTION
1 MAX THROW
2 X-AXIS CENTRALITY
3 GAP WITH MAX. THROW
Key Pad Control
Operation of the CAG system is achieved by a 16- position key pad in conjunction with a menu-driven CRT display. Depending on the type of application, and the software developed for it, the operator can be told which task to perform, or be given a choice of actions. In certain applications the operator will answer YES/NO or key in the appropriate number, then ENTER, and the system advances to the next step.
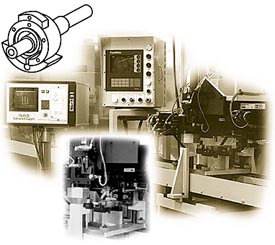
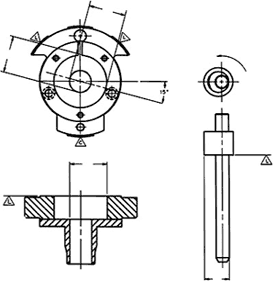
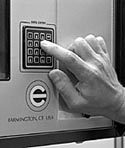




A New Dimension In Precision Measurement
.
(860) 677-2813

Toll Free 877-521-5818